The food processing facility was dealing with water intrusion from a failing EPDM roof that was putting the integrity of their products and operation at risk.
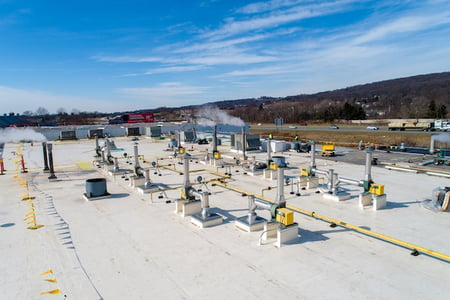
Project Story:
Dawn Foods supplies a complete line of quality, consistent mixes, bases, icings, glazes, fillings, frozen dough, par-baked and fully baked products and equipment to the food industry — worldwide. Their food production facilities are where the magic happens and protecting the delicious desserts from water intrusion is critical to the quality of bakery products.
Wes Hertel, Maintenance Manager at the York, Pennsylvania Dawn Foods production plant said the facility’s 640-square, 26-year old ballasted EPDM roof was failing, and they were experiencing a lot of leaks. “We just absolutely cannot have water leaks inside a food production facility,” said Hertel. “Water and food products don’t mix.”
Hertel said it took some time for him to get approval for a new roof, but when he finally did, he wanted a system that would withstand the high foot traffic and be resistant to the greases that can come out of the exhaust systems on the roof. The facility has to check their systems on a daily basis, and they are all located on the roof. He said some of the other plants had installed TPO roofs, but he was searching for a system that would provide the highest puncture resistance possible and the best protection against grease.
Chris Hall, Vice President of Heidler Roofing, met with Hertel to listen to what his pains were and help find the right solution. “With all the foot traffic and different contaminants that come out of the exhaust systems I knew that the durability of a FiberTite system would be the right fit,” explained Hall. “The puncture resistance is great, and the grease and chemical resistance is great as well. Other systems are just going to wrinkle up and have issues because of chemical exposure, but the FiberTite system really stands up to this environment.”
FiberTite Roofing Systems provide superior resistance to volatile exhaust from animal fats, cooking oils and greases. The systems are also engineered to withstand severe weather and environmental forces.
Hall turned to FiberTite sales representative Kevin Cooper to meet with Hertel to review the product samples and different systems. “We met with Wes, and he knew this was the right system to meet the facility’s needs,” said Cooper. “He asked us to come back to do a presentation to the board. We brought our puncture kit to demonstrate the durability of the various membrane options. The board agreed with Wes’s choice and selected the 45-mil FiberTite-SM membrane system.”
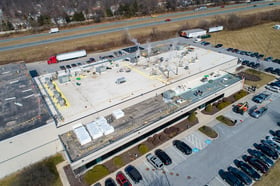
45-mil FiberTite-SM features an 18 x 19 / 840 x 1,000 denier weft reinforced polyester knit fabric, coated with a proprietary compound, utilizing ELVALOY™ Ketone Ethylene Ester as the principal polymer in the hybrid vinyl alloy coating. The membrane is coated on the face with Seaman Corporation’s original “ELVALOY™ KEE” formulation to provide superior hot air welding characteristics, extreme UV resistance, broad chemical resistance and long-term flexibility and reparability for the installed roofing membrane system.
Installation began in 2018 and the Heidler Roofing crew faced a challenging installation, having to work around the many penetrations, curbs and vent pipes, not to mention the record amount of rainfall that fell in 2018. After removing the ballasted EPDM system, the crews installed fully-adhered, three-inch polyiso insulation followed by an adhered layer of DensDeck to ensure maximum durability against the high volumes of foot traffic. The membrane was then fully adhered, and seams welded to ensure watertight protection for the plant. “The roof comes with a 20-year system warranty, but the longevity of the system will be well past those 20 years,” concluded Cooper.
This project profile was written by a contributor from Roofers Coffee Shop.
ELVALOY™ is a trademark of The Dow Chemical Company (“Dow”) or an affiliated company of Dow.